Acorn Deck House Company Featured in Wicked Local Article
Wicked Local journalist Molly Loughman approached us for an article in the Acton-Boxborough Beacon, which was published April 9, 2015. Read the full article below.
Acorn Deck House Company Offers Custom Architecture
For people desiring unique architecture in building their custom dream home, Acorn Deck House Company (ADHC) helps people actualize those desires by designing, building and maintaining prefabricated homes.
Headquartered in Acton at 852 Main St., ADHC provides a comprehensive design process with refined building systems, manufactured to specifications and the clients’ requirements before the parts are delivered to the construction site. With 59 ADRHC homes in Acton, 42 in Boxborough and more than 200 internationally, the company has built 20,000 worldwide.
Acorn Deck House Company offers multiple home building options, with most designs categorized into three styles, all of which feature open floor plans, walls of glass and ceilings which can be customized for the individual client and building site.
“The original was solid beams. Now we’ve gone to laminated beams, which increases the constructional strength of the house and gives us greater options for expanding. Manufacturing is a great option because the materials we use here are used in-house so we can control what gets used in the house during construction time. We use a lot of our own waste products,” said general manager Paul Buraczynski, noting computerized numerical control (CNC) machines are used for precision in cutting material. “We really strive hard to cater to having the houses built with the best views. We build houses within cities; we build houses on top of mountains, on the ocean — anyplace. They’re everywhere.”
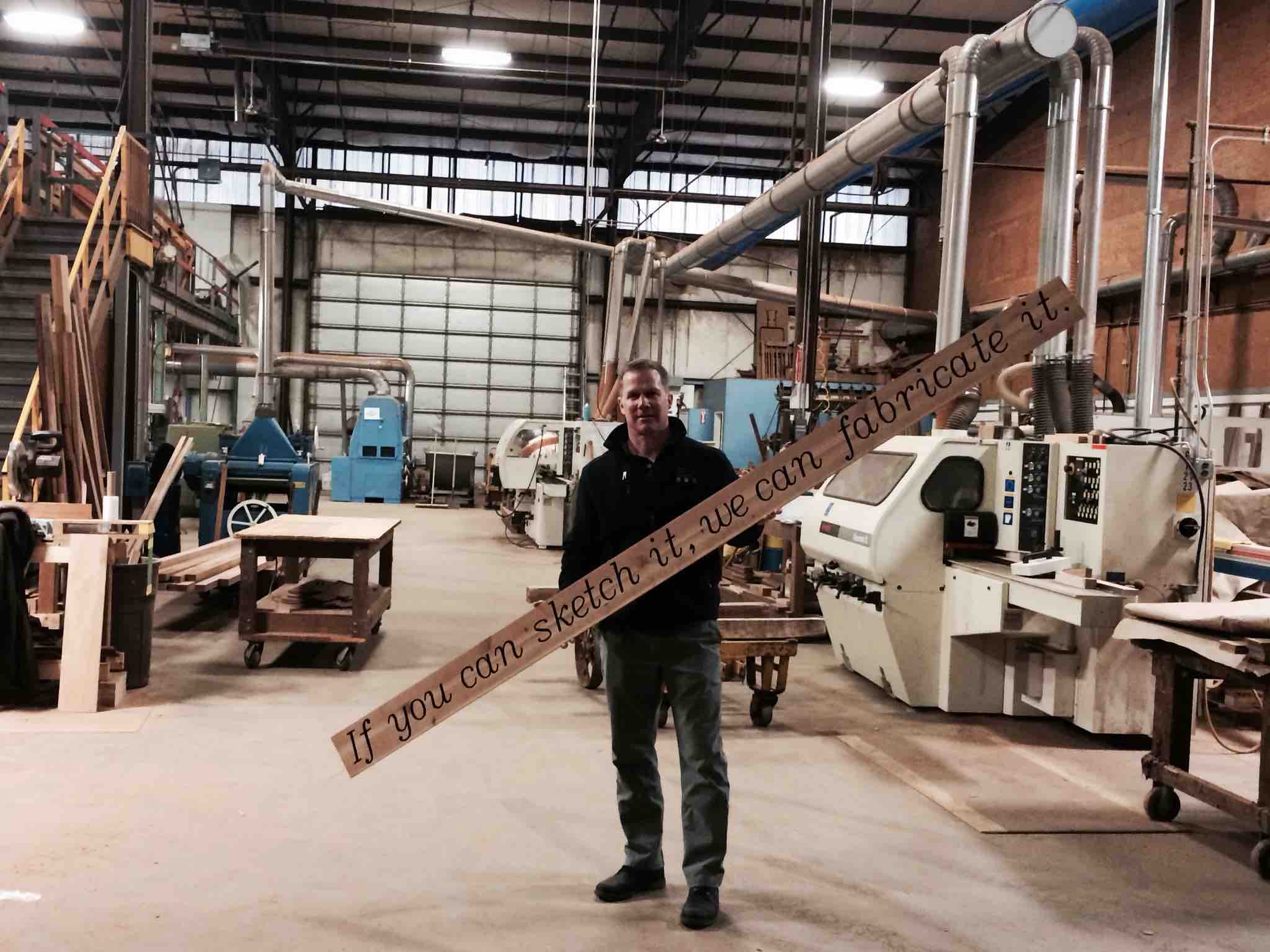
Wicked Local Staff Photo by Molly Loughman
The company completes between 30 and 40 building projects each year, with homes made in its 85,000-square-foot manufacturing plant located behind the ADHC model home office off Main Street. It takes two weeks to manufacture a house after it has been designed.
Inspired by traditional New England architecture, the Acorn Home has a contemporary twist. Its post-and-beam interior allows for an open plan because the interior partitions are not required for support.
The Deck House features post-and-beam construction inside and out with exposed Douglas fir beams, natural wood ceilings of cedar decking and mahogany windows and trim. The NextHouse is based on the Deck House system, but with a modernist interpretation.
“We still work with all the old houses that are out there from the beginning. We’re still here to help and do any replacement product on the house. We still care about all those customers and they care about us, too,” said Buraczynski.
ADHC also offers a collaboration program, which is a working relationship with independent architects to produce a custom, prefabricated home.
“We’re very interesting to architects because some of the materials we have here and we also manufacture our own mahogany windows, a very contemporary style, which a lot of architects are drawn toward. Acton has been a great hub for us. It’s close to shipping ports.“said Buraczynski, noting that moving forward, the company hopes to go full solar manufacturing with a solar-paneled roof.
Owner support services include design services and materials, toll-free assistance for maintenance and repair instructions, spare and replacement parts and special services and pricing for repeat buyers.
“I like the whole concept of the pre-engineered. It’s something really different and adds a lot in terms of quality because things are done under factory conditions. So many incidences you’ll see the materials were left outside and then when the house is built, the quality just isn’t there,” said project director Diane Williams. “We have a really talented design group here, but our objective is to build a house, so we’re not going to design something outside of someone’s budget.”
ADHC homes are intended to be environmentally conscientious with an emphasis on passive solar benefits, tight construction and controlled, waste-minimizing manufacturing processes.
“We cater to what the customers want. We have a net-zero house that we’re looking at building for our model home in Acton. We own the land right now and just put the permits in to start building it. It has triple-glazed windows, extra insulation,” said Buraczynski, noting the company must meeting changing building codes in every state and country it’s clients are from. “We’re always striving to be better, meet codes and push the engineering envelope as far as we can to make a custom house that someone is creating that they want. We’re a very creative company and our goal is to give someone their dream house.”
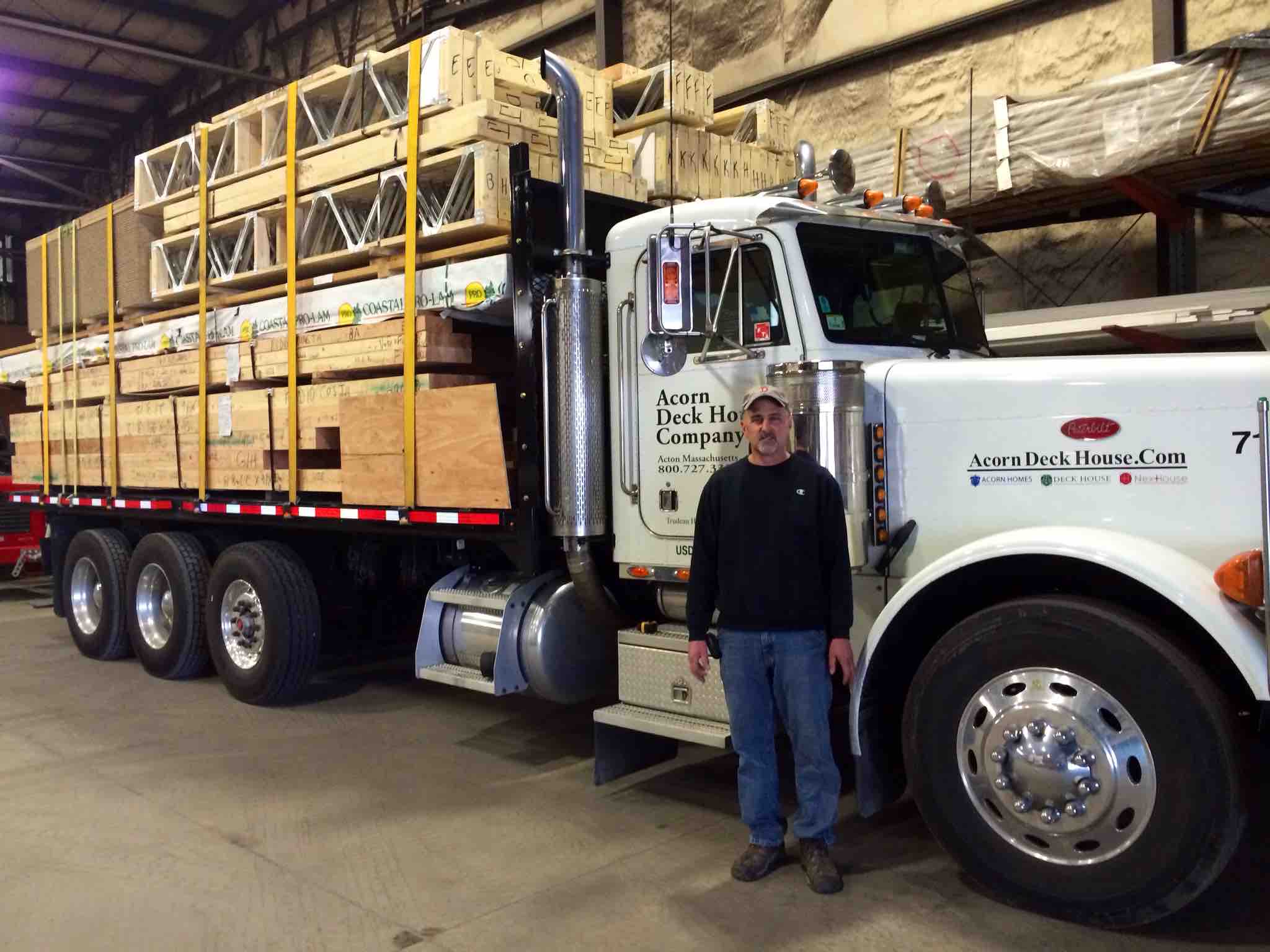
Wicked Local Staff Photo by Molly Loughman